The LCD screen is at the highest level of the entire liquid cooling system. After the first few prints, the coolant heats up and may cause deformation of the LCD screen. If deformation takes place, please use the pressure release cap on the coolant tank to rebalance the pressure.
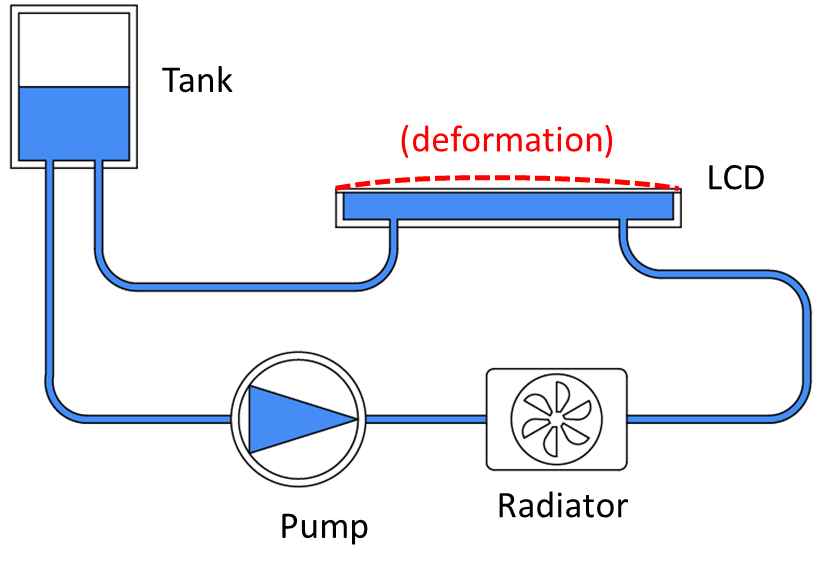
Tools Required:
1. Standard Ruler;
2. Feeler Gauge;
3. Wrench;
Note:
1. For the user’s safety, please power off the printer before this operation!
2. Check the LCD every two weeks as advised.
1、Put the printer on table and open the cover
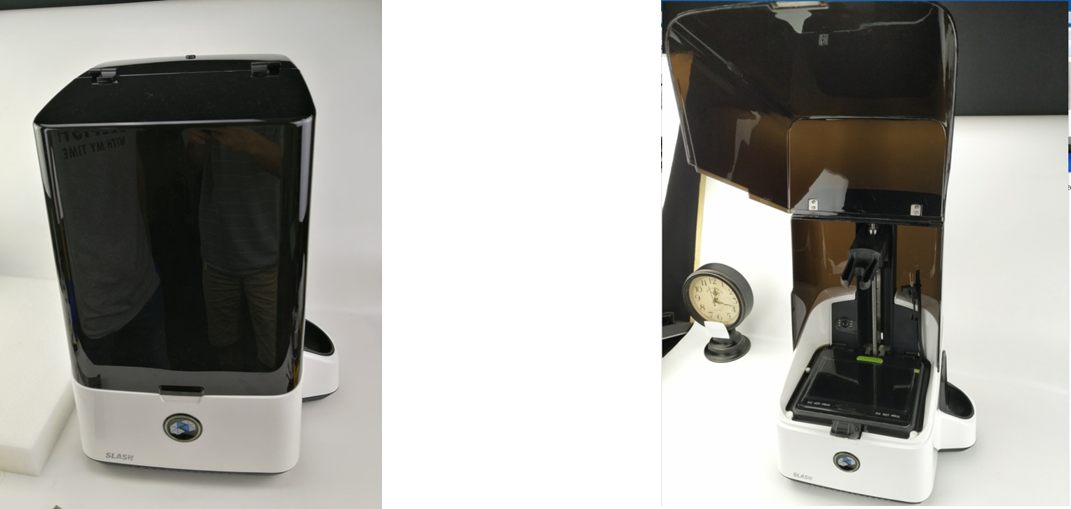
2、Check if the pressure is normal in the screen cooling system
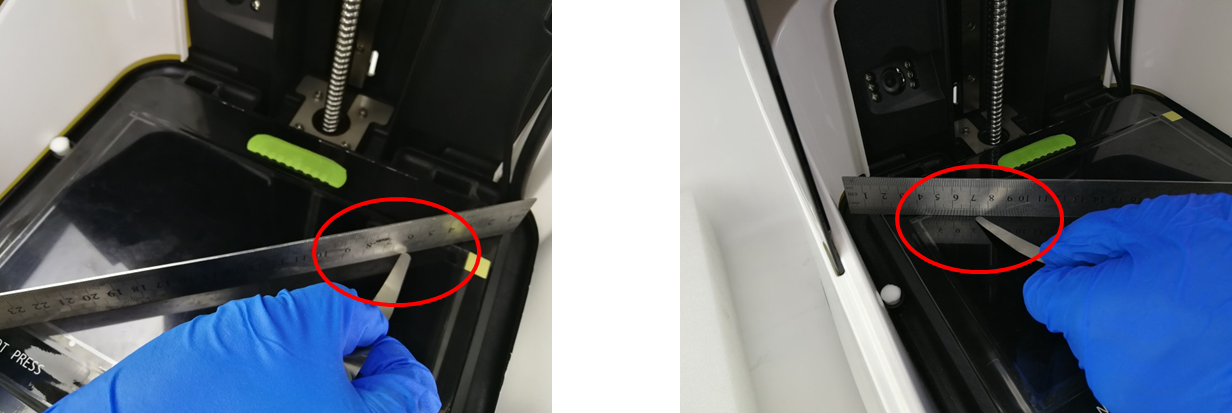
If there is no gap between the ruler and the screen, it is NOT necessary to release the pressure.
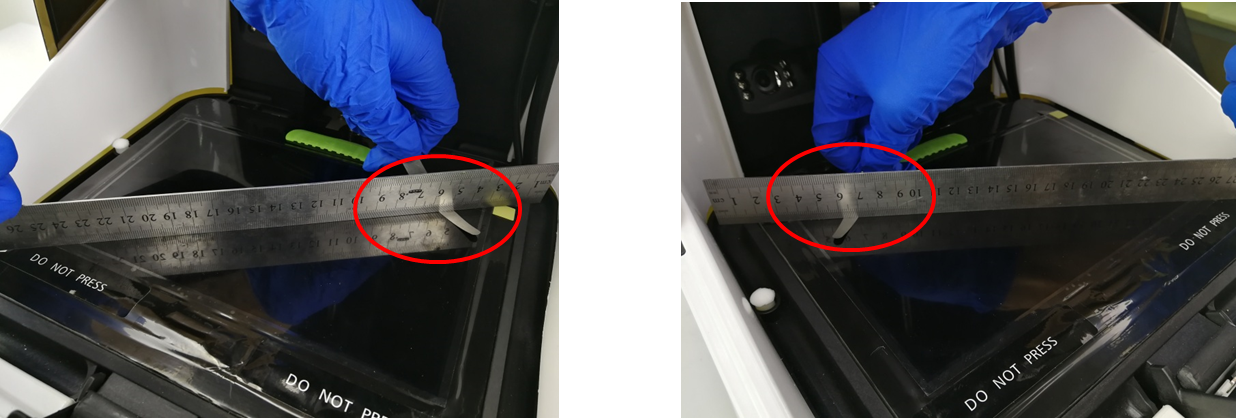
If there is gap between the ruler and the screen, it is necessary to release the pressure.
3、Put the printer sideways
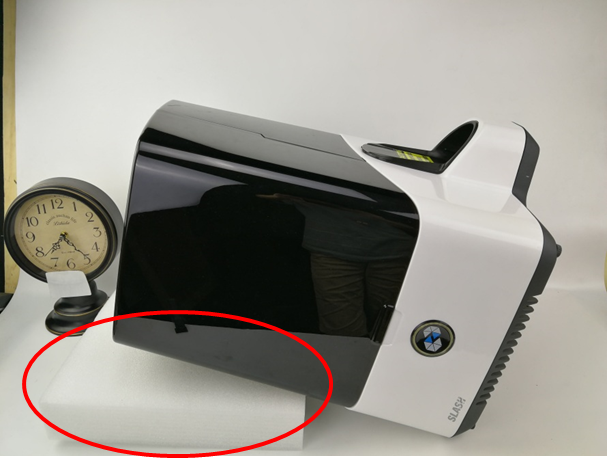
Lay protections to prevent possible damage to the printer
4、Remove the ties and push out the coolant tank
5、Take off the coolant tank
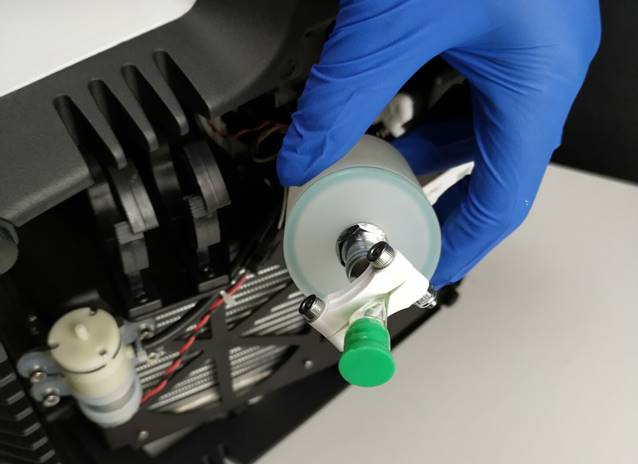
Take off the coolant tank from the holder
6、Remove the joint of the coolant tank to release the pressure
Prepare some tissue to wipe off the coolant which may spill out of the tank; do not keep any electronic device near the printer
7、Squeeze the tube and tighten the joint
Tighten with suitable strength
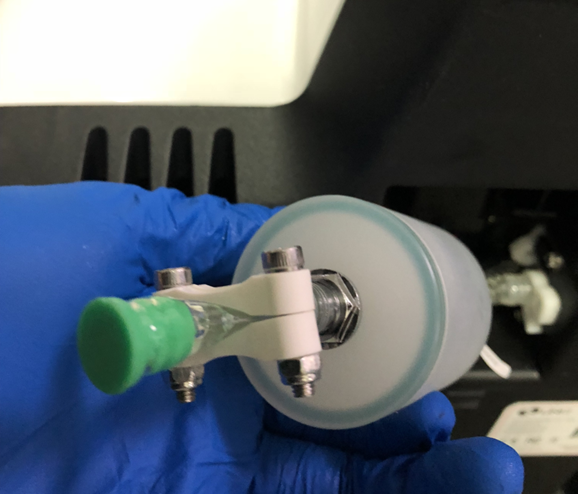
Wipe clean the coolant tank and the tubes
8、Put back the coolant tank to the holder
Press tight the holder as the arrows show in the picture; make sure they are centered and match each other effectively
9、Put back the nylon ties
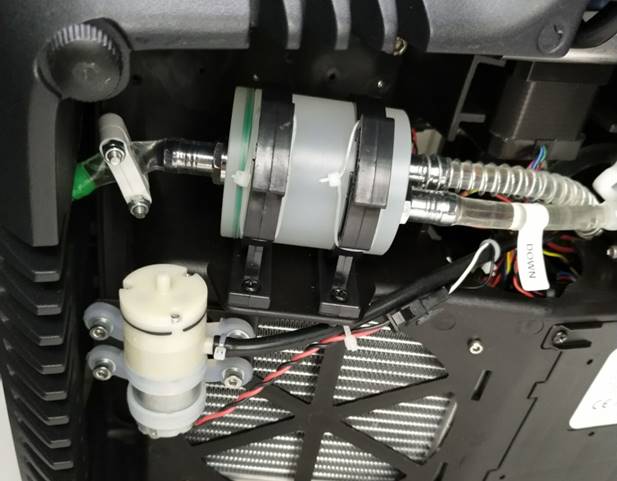
Fixate the holder with nylon ties
10、 Put the printer upright
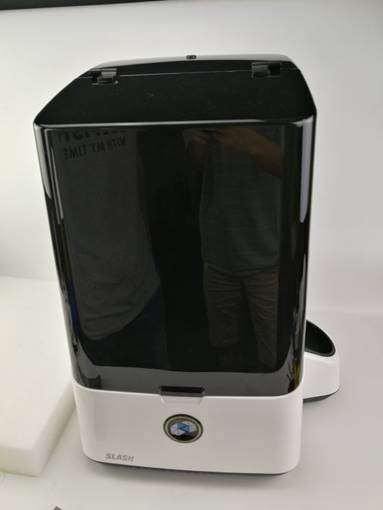
11、The pressure in the screen cooling system has been normal
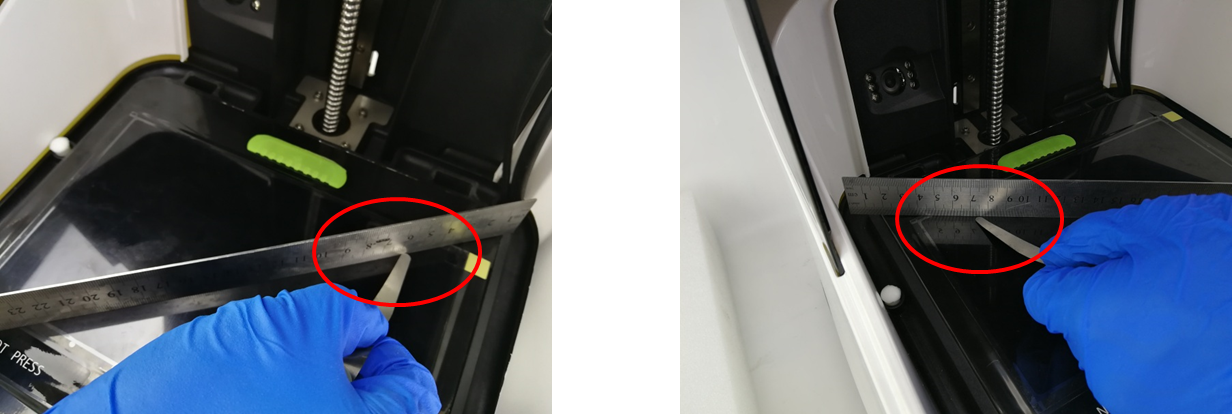
Test with feeler gauge and there is no gap
12、Finished
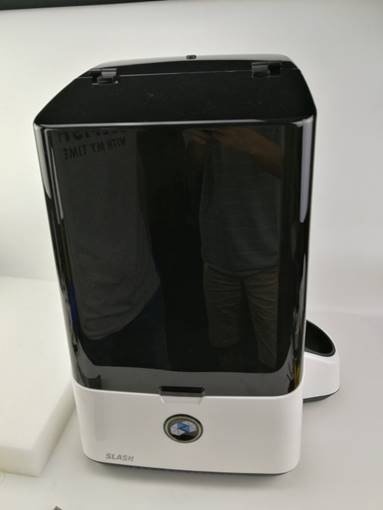